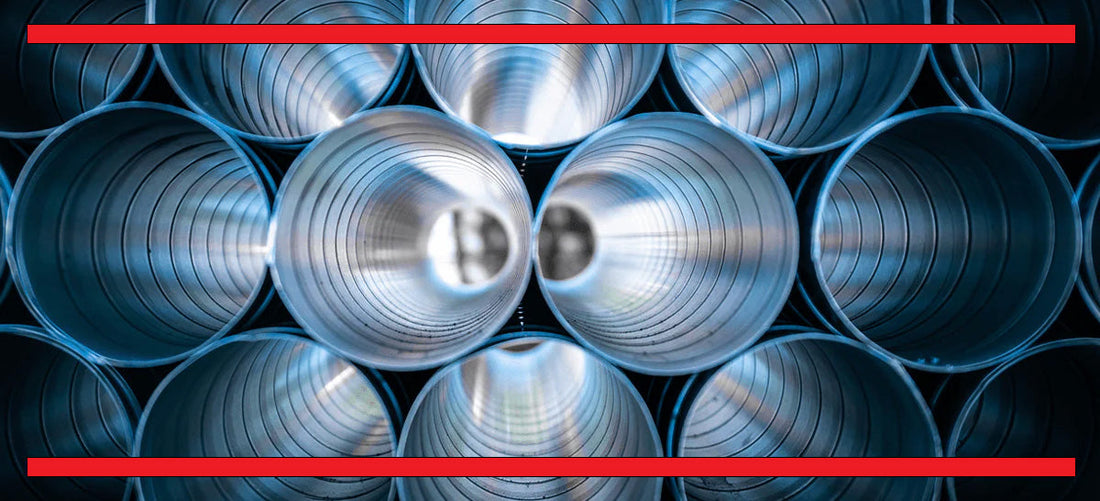
Pipe Fabrication Turnarounds
Share
Shutting down for maintenance is common for most plants. These “turnarounds” give the facility time to inspect equipment and perform repairs. Proper planning and execution can have a positive impact on turnaround outcomes. A poorly implemented turnaround can affect efficiency, service delivery and profits.
Pipe fabrication is integral to turnaround projects. Installing, repairing or replacing pipes is a large part of the maintenance process. Efficient, high-quality pipe fittings contribute to a turnaround's success.
Explore how efficient pipe fabrication turnarounds can optimize your business operations.
What Are Pipe Fabrication Turnarounds?
These turnarounds are closures of a plant's operations for pipe maintenance. The activities performed include inspection, cleaning, repair, replacement or installation of new pipes.
Pipelines are integral to industries like oil and gas, energy and aerospace. Well-maintained pipes are especially important when they contain hazardous substances.
There are three types of pipe fabrication turnarounds:
- Planned: A plant closure for scheduled maintenance or repair. Most plants operate on a three to five-year turnaround cycle.
- Construction: Pipe fabrication as part of a new build or extension to an existing plant.
- Unplanned: An emergency, like a pipe explosion, can cause an unscheduled turnaround. Operations typically halt for as long as it takes to repair or replace the pipe.
Speed and efficiency are crucial during plant shutdowns. Extended closures result in decreased productivity, increased labor costs and reduced profits.
The 5 Phases of Manufacturing Turnarounds
Turnarounds include five critical phases:
- Scoping: Planning of timelines, budget and affected assets happens during this first phase.
- Preparation: The details gathered in the scoping phase inform a detailed turnaround plan. Its complexity and many moving parts make this the lengthiest phase of a turnaround project.
- Execution: This is the implementation phase. Contractors, welders and workers carry out the planned activities. The execution stage is the shortest but most challenging.
- Startup: Before operations resume, a final inspection confirms the readiness of the equipment. Pipes must be well-aligned and properly joined. Executing procedures for the first time since shutdown increases safety risks.
- Review: A post-turnaround review assesses success and failures. These often inform root-cause analyses and corrective actions.
Essential Components of a Successful Turnaround
The pillars of successful turnarounds are planning, preparation, supplier relations, quality control, tooling, training, execution, risk management, constraint management and supervision.
Here's how to ensure project management success:
1. Plan Ahead
Planning may be the most critical contributing factor to turnaround success. A shutdown is no small feat, and planning should start eight to 12 months before the execution date. This allows enough time to set objectives, devise strategies and outline goal-oriented tasks.
Well-planned turnarounds minimize downtime and safety risks. A turnaround plan should consider the following:
- Resource allocation: Turnaround resources include people, equipment, time and budget.
- Project scheduling: Establishing a timeline with key milestones optimizes downtime. A project schedule should include who is doing what and when.
- Key performance indicators (KPIs): KPIs gauge the project's success against objectives.
2. Prioritize Risk Management
Risk management is also crucial for turnarounds. The complexity of these projects involves safety, operational and financial risks. Risk management identifies possible threats and establishes measures to mitigate them.
Even the most well-planned metal fabrication turnarounds experience unforeseen obstacles. Preparing for the unexpected involves identifying possible variables and making contingencies. Pausing a project to order parts or tools can cause delays that extend downtime. Mitigation plans could involve stockpiling components or a diverse toolkit for any task.
3. Establish Subcontractors Early
Early collaboration with trusted suppliers enhances turnaround success. In pipe fabrication, this may entail hiring welders or consulting with tool providers. Ordering specialized tools or parts beforehand ensures readiness when the project begins.
4. Ensure Quality Control
Quality control is critical in metal fabrication turnarounds. Ineffective pipe welding management can result in costly reworks or more severe consequences. A leak from misaligned pipes can spell disaster in the oil and gas industry.
Maintaining quality control means selecting skilled tradespeople with accountability for their areas. Develop and communicate a strategy to stakeholders in advance. Part of this plan includes a post-turnaround inspection with a quality assurance manager.
Use only high-quality parts and components. Opting for inexpensive or low-quality items can impact project success and safety. Pipe alignment tools provide significant quality advantages during fabrication turnarounds. Clamps ensure precise alignment and joining of pipelines for more reliable results.
5. Minimize Safety Hazards
Complex tasks, tight deadlines, and additional contractors heighten turnaround safety risks. Address these risks by:
- Risk assessment: Identify possible hazards early on and determine how to mitigate them.
- Training: All stakeholders, including contractors, need training in equipment use and safety.
- Safety protocols: Implement strict safety procedures and conduct regular audits.
- Personal protective equipment (PPE): Ensure all project participants have appropriate PPE.
- Communication: Maintain constant communication with workers on safety standards, near-misses or stand-downs on incidents that have occurred.
6. Recognize Areas of Opportunity
A turnaround provides a valuable opportunity to upgrade systems and increase efficiencies. Strategic, well-planned projects can leave your facility better than it was before.
Manufacturing turnarounds are often a learning curve. Obstacles, successes and failures can identify ways to improve processes for the future.

How Pipe Fitting Tools Enhance Turnaround Efficiency
Walhonde Tools leads in pipe alignment technology that speeds up turnarounds. Here's how pipe fitting tools benefit these projects:
- Saves time: Fit-ups and alignment can take considerable time. Walhonde pipe fitting tools can reduce pipe joining tasks from hours to minutes. Welders and pipe fitters can solve fitting problems in minutes with our tools. Ovality correction reduces fit-up time.
- Saves money: Correcting a misaligned pipe requires precious minutes, labor and materials. Pipe alignment tools get the job done right the first time with precision, therefore reducing unplanned costs associated with reworks or repairs. The more efficient the pipe joining process, the sooner you can get your plant up and running again.
- Ensures quality pipe welding: Our tools achieve accurate spacing and alignment for quality welds.
- Maintains integrity: Precise joint welds ensure the structural integrity of pipe systems.
- Increases safety: Pipe alignment tools safeguard workers by preventing pipe displacement. Pipeline leaks are catastrophic in many industries. Reliable joining prevents leaks, increasing safety for people and the environment.
Optimize Turnarounds With Walhonde Tools
For over 30 years, Walhonde Tools has enhanced efficiency in turnarounds and pipe fitting. Our patented pipe alignment tools boost productivity, quality and safety. We offer precision tools for pipe welding, fabricating or repair.
Our Top Liner™ range is available for rent or purchase. Choose from:
- Top Liner™: For accurate spacing and high-low alignment, choose Top Liner. This heavy-duty clamp fits pipes from 2 to 72 inches with any wall thickness or schedule.
- Top Liner™ Elite: This clamp has a 10-degree left or right clocking feature. It offers precise control for fitting, neck flange, elbow, or clocking pipe applications.
- Top Liner™ Gen III: Top Liner Gen III offers controlled welding for minimal pre-load fit-ups. Use it for pipe-to-pipe, tee-to-pipe, flange-to-pipe or elbow-to-pipe jobs.
Increase efficiency on your next pipe fabrication turnaround. Contact us online to learn more.